
“This project started in 2018 with PAG and Institut für Verbundwerkstoffe (IVW, Kaiserslautern, Germany) to show what is possible with thermoplastic composites in large parts and primary structures,” explains Dr.
#TARGET WELD IN WINGS 3D MANUAL#
The prefabricated semi-permeable membrane was applied in a semi-automated way via an end-effector with an “umbrella-like” mechanism, while placement of tacky tape and outer vacuum bag remained manual but could also be automated.

“They didn’t have to be draped, just placed,” notes Malecha. Vacuum bagging auxiliary materials - peel ply, perforated release film and resin flow media (tool-side auxiliary materials) - were precut and prejoined, designed for where they were placed. This gripper comprises three small and independent 6-degrees-of-freedom (DOF) robots and a rigid arm, all mounted on the center flange of an industrial 6-DOF robot. For this task, the Multi Kinematic Gripper was developed and was also used to apply the vacuum bag auxiliary materials. After completing the preform, eight stiffeners (stringers) were attached on top. 1 from “Highly Automated Manufacturing Process of Large Airplane CFRP Structures” by Marcin Malecha and Thomas Full, Center for Lightweight Technology (ZLP), German Aerospace Center (DLR). Photo Credit: German Aerospace Center (DLR) Institute of Structures and Design Marcin Malecha, project manager for PROTEC NSR at DLR.ĭiagram of the types of cut-pieces and stringers applied to create the preform for the RPB demonstrator manufactured by DLR in the PROTEC NSR project.
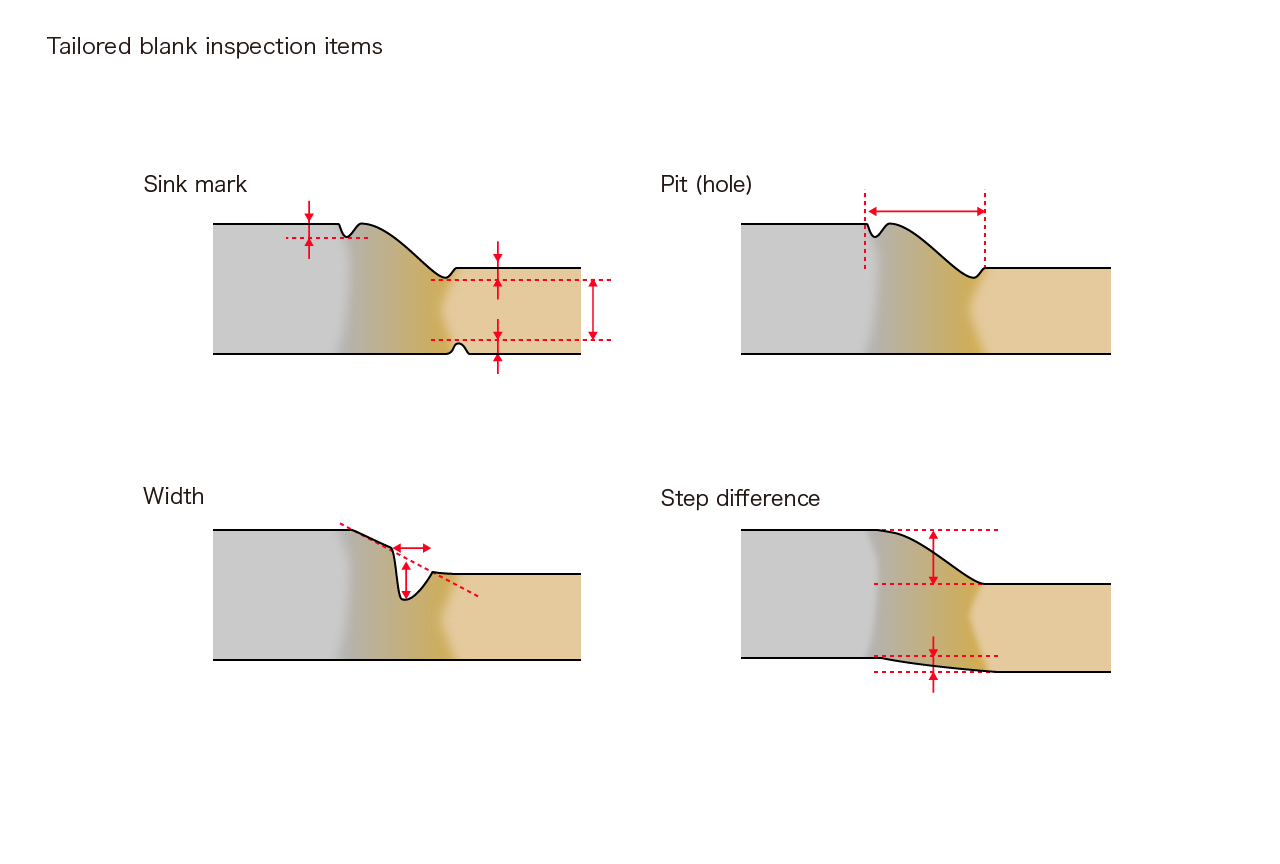
“Our first automation solution was for layup, and then we worked to automate more operations.” The main goal for PROTEC NSR was to take these specialized solutions for RPB production and bring them into a single automated process, explains Dr. Lars Larsen, head of assembly and joining technologies at ZLP Augsburg.
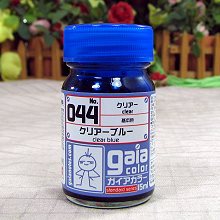
“We started many years ago with PAG in the AZIMUT project to analyze manual processes for composites manufacturing,” says Dr. Both projects worked with the Tier 1 supplier of these structures, Premium Aerotec Group (PAG, Augsburg, Germany), and demonstrated automation while evaluating cycle time and cost. The German Aerospace Center (DLR) Institute of Structures and Design operates the Center for Lightweight Production Technology (ZLP) in Augsburg. Among its many composites manufacturing projects, PROTEC NSR and Fast Lane RPB present a unique opportunity to compare, respectively, a liquid-molded thermoset rear pressure bulkhead (RPB) for the twin-aisle Airbus A350 with a thermoplastic RPB for the single-aisle Airbus A320. But how do they compare?ĭifficult Materials Make Automated Fabric Cutting More Indispensable than Ever
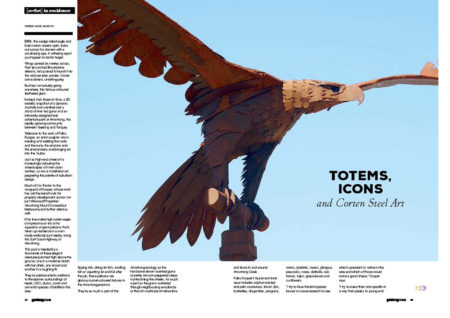
These programs use automation to increase production rate and quality while reducing cost. The second is thermoplastic composites (TPC) featured, for example, in the Clean Sky 2 Multifunctional Fuselage Demonstrator (MFFD), where stiffened skins are created using automated fiber placement - in-situ consolidated for the upper half and autoclave-consolidated for the lower half - followed by assembly via welding. The first is liquid molding of dry fiber preforms seen, for example, in Spirit AeroSystem’s (Prestwick, Scotland) high-rate resin transfer molding (RTM) line for Airbus A320 spoilers and also in the Airbus-led Wing of Tomorrow (WOT) program which uses automated placement of noncrimp fabrics (NCF) and liquid resin infusion, followed by out of autoclave (OOA) cure in an oven (see “ High-rate, automated aerospace RTM line delivers next-gen spoilers” and “ Update: Lower wing skin, Wing of Tomorrow” respectively.) Photo Credit: German Aerospace Center (DLR) Institute of Structures and DesignĪs OEMs and suppliers explore the materials and processes that will enable the next generation of aircraft, two different approaches are being demonstrated. In a separate project, eight “petal” sections were press-molded from CF/PPS organosheet and ZLP used automated resistance welding to form an A320 RPB (right). The DLR Center for Lightweight Production Technology (ZLP) has demonstrated an automated process for an A350 rear pressure bulkhead (RPB) using dry CF fabric (left) and resin infusion with Hexcel’s RTM6 epoxy.
